Making sure the machine frame is flat enough, straight enough and parallel enough for profiled rails to be correctly mounted is no small task. In fact, the frame geometry itself can make it challenging to mount bearing rails parallel to one another in either the horizontal or vertical axis, or both. The result? Rolling elements and raceway surfaces are unevenly loaded, leading to pitting, noise issues and premature bearing failure. To avoid this, machine builders often spend significant time and money on surface preparation and machining to make sure bearing rails can go on perfectly straight and flat. But is all this preparation really necessary? Some high-end motion applications may call for exceptionally flat, straight and parallel mounting surfaces, but the truth is that most do not.
Another approach to handling misalignment and its associated problems is to use a self-aligning linear guide such as Rollon’s Compact Rail. This system is inherently forgiving of misalignment due to a unique rail geometry that compensates for alignment errors in one or two axes. In contrast to the demanding installation requirements for profiled rail, Compact Rail features large rolling elements, rail profiles that allow some play and an easy preload adjustment that enables equal loading of all elements. In other words, you get a more compliant guide than a profiled rail—and one that can align itself to less than perfect mounting surfaces.
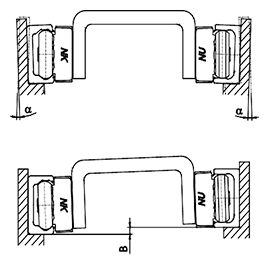
It’s important to keep in mind that these two approaches—using high-precision profiled rail or a self-aligning system—can coexist in the same machine. For example, a machine tool spindle may demand a perfectly accurate linear motion system whereas a tool changer does not. Choosing the right linear guide for each axis based on individual requirements for precision and accuracy can save costs and achieve smooth, reliable linear motion at the same time.
A final point to keep in mind is contamination. With profiled rail, the small recirculating balls in the raceway have extremely limited clearance—meaning that even tiny pieces of dirt can interfere with motion. Bearings with larger diameter rollers such as those in Compact Rail can easily roll over much larger pieces of debris with no ill effects.